Покрытия и их свойства и противопоказания
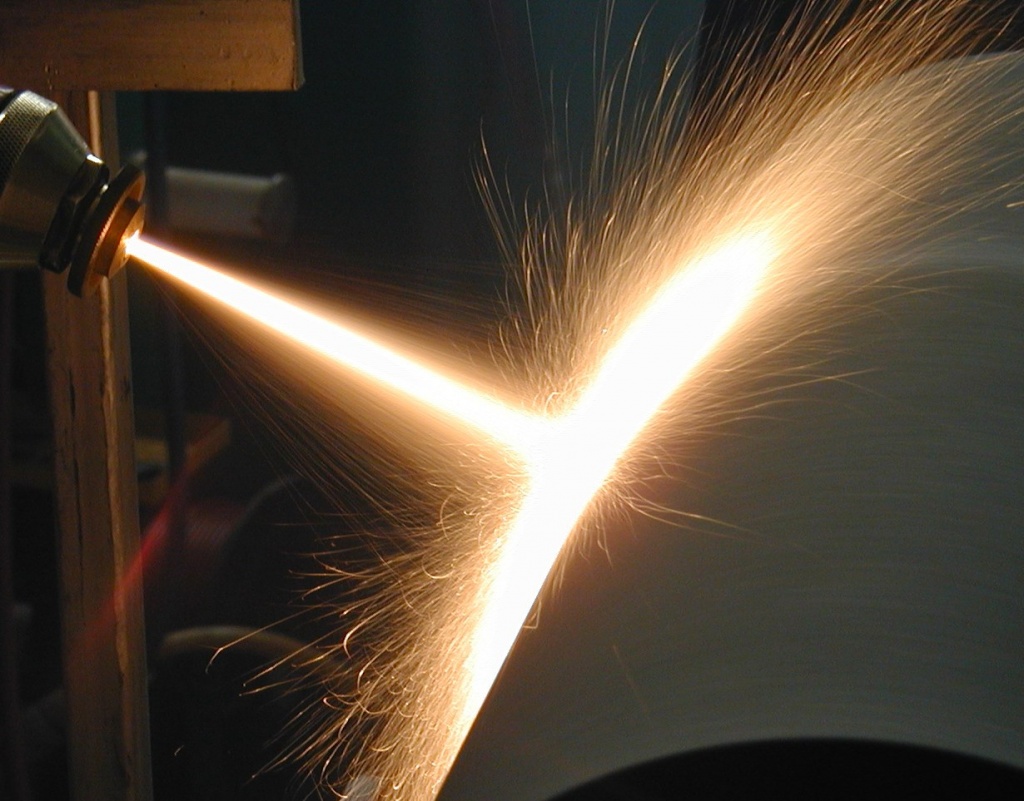
Уникальной разновидностью неметаллических защитных покрытий являются антифрикционные материалы. По внешнему виду они напоминают краски, однако вместо пигментов содержат частицы твердых смазочных веществ, которые равномерно распределены в смеси связующих компонентов и растворителей.
В противокоррозионной практике для изоляции металла от воздействия агрессивных сред используются специальные защитные покрытия. Все они подразделяются на металлические и неметаллические.
Металлические – анодные и катодные – покрытия наносятся на поверхности методами газотермического напыления, окунания, гальванизации, плакирования или диффузии.
К неметаллическим защитным покрытиям относятся лакокрасочные составы, полимерные пленки, силикатные эмали, резины, оксиды металлов, соединения фосфора, хрома и др.
Рассмотрим все виды покрытий подробнее.
Металлические защитные покрытия
В качестве анодных металлических покрытий выступают металлы, электрохимический потенциал которых меньше, чем у обрабатываемых материалов. У катодных он, наоборот, выше.
Анодные покрытия обеспечивают электрохимическую защиту металлических поверхностей и выполняют свои функции даже при нарушении целостности слоя.
Катодные покрытия препятствуют проникновению агрессивных сред к основному металлу благодаря образованию механического барьера. Они лучше защищают поверхности от негативных воздействий, но только в случае неповрежденности.
В зависимости от способа нанесения металлические покрытия подразделяются на следующие виды.
Гальванические покрытия
Гальванизация – это электрохимический метод нанесения металлического защитного покрытия для защиты поверхностей от коррозии и окисления, улучшения их прочности и износостойкости, придания эстетичного внешнего вида.
Гальванические покрытия применяются в авиа- и машиностроении, радиотехнике, электронике, строительстве.
В зависимости от назначения конкретных деталей на них наносятся защитные, защитно-декоративные и специальные гальванические покрытия.
Защитные служат для изоляции металлических деталей от воздействия агрессивных сред и предотвращения механических повреждений. Защитно-декоративные предназначены для придания деталям эстетичного внешнего вида и их защиты от разрушительных внешних воздействий.
Специальные гальванические покрытия улучшают характеристики обрабатываемых поверхностей, повышают их прочность, износостойкость, электроизоляционные свойства и т.д.
Разновидностями гальванических покрытий являются меднение, хромирование, цинкование, железнение, никелирование, латунирование, родирование, золочение, серебрение и пр.
Газотермическое напыление
Представляет собой перенос расплавленных частиц материала на обрабатываемую поверхность газового или плазменным потоком. Покрытия, образованные таким методом, отличаются термо- и износостойкостью, хорошими антикоррозионными, антифрикционными и противозадирными свойствами, электроизоляционной или электропроводной способностью. В качестве напыляемого материала выступают проволоки, шнуры, порошки из металлов, керамики и металлокерамики.
Выделяют следующие методы газотермическогого напыления:
- Газопламенное напыление: самый простой и недорогой метод, применяемый для защиты крупных площадей поверхности от коррозии и восстановления геометрии деталей
- Высокоскоростное газопламенное напыление: используется для образования плотных металлокерамических и металлических покрытий
- Детонационное напыление: применяется для нанесения защитных покрытий, восстановления небольших поврежденных участков поверхности
- Плазменное напыление: используется для создания тугоплавких керамических покрытий
- Электродуговая металлизация: для нанесения антикоррозионных металлических покрытий на большие площади поверхности
- Напыление с оплавлением: применяется тогда, когда риск деформации деталей отсутствует или он оправдан
Погружение в расплав
При использовании этого метода обрабатываемые детали окунаются в расплавленный металл (олово, цинк, алюминий, свинец). Перед погружением поверхности обрабатываются смесью хлорида аммония (52-56 %), глицерина (5-6 %) и хлорида покрываемого металла. Это позволяет защитить расплав от окисления, а также удалить оксидные и солевые пленки.
Данный метод нельзя назвать экономичным, так как наносимый металл расходуется в больших количествах. При этом толщина покрытия неравномерна, а наносить расплав в узкие зазоры и отверстия, например, на резьбу, не представляется возможным.
Термодиффузионное покрытие
Данное покрытие, материалом для которого выступает цинк, обеспечивает высокую электрохимическую защиту стали и черных металлов. Оно обладает высокой адгезией, стойкостью к коррозии, механическим нагрузкам и деформации.
Слой термодиффузионного покрытия имеет одинаковую толщину даже на деталях сложных форм и не отслаивается в процессе эксплуатации.
Плакирование
Метод представляет собой нанесение металла термомеханическим способом: путем пластичной деформации и сильного сжатия. Чаще всего таким образом создаются защитные, контактные или декоративные покрытия на деталях из стали, алюминия, меди и их сплавов.
Плакирование осуществляется в процессе горячей прокатки, прессования, экструзии, штамповки или сваривания взрывом.
Виды и особенности неметаллических покрытий
Неметаллические покрытия подразделяются на органические и неорганические. Они создают на обрабатываемых поверхностях тонкую, инертную по отношению к агрессивным веществам пленку, которая предохраняет детали от негативных воздействий окружающей среды.
Лакокрасочные защитные покрытия
В состав таких покрытий входят пленкообразующие вещества, наполнители, пигменты, пластификаторы, растворители и катализаторы. Варьирование состава позволяет получать материалы со специфическими свойствами (токопроводящие, декоративные, особопрочные, жаростойкие и т.п.). Они не только защищают изделия в различных условиях, но и придают им эстетичный внешний вид.
В группу лакокрасочных покрытий входят лаки, краски, грунтовки, олифы, шпаклевки.
Силикатные эмали
Применяются для изделий, работающих при высоких температурах в химически агрессивных средах.
Эмалевое защитное покрытие формируется с помощью порошка или пасты. Процесс проходит в несколько этапов. Сначала на изделие наносится грунтовая эмаль – она улучшает адгезию, уменьшает термические и механические напряжения.
Затем, после спекания первого слоя при температуре +880… + 920 °С, накладывается покровная эмаль, после чего изделие снова подвергается нагреванию до +840… +860 °С.
Если требуется нанести несколько слоев силикатной эмали, вышеописанные операции проводят поочередно несколько раз. Изделия из чугуна, к примеру, обрабатывают в 2-3 подхода.
Застывшая эмаль представляет собой тонкое, похожее на стекло, покрытие. Его основным недостатком является сравнительно низкая прочность – под воздействием ударных нагрузок эмаль может растрескиваться или скалываться.
Полимерные защитные покрытия
В число наиболее распространенных полимеров, применяющихся для защиты металлов от коррозии, входят полистирол, полиэтилен, полипропилен, полиизобутилен, фторопласты, эпоксидные смолы и др.
Полимерное покрытие осуществляется методами окунания, газотермического или вихревого напыления, обычной кистью. Остывая, оно образует на поверхности сплошную защитную пленку толщиной несколько миллиметров.
Разновидностью полимерных являются антифрикционные твердосмазочные покрытия. Внешне эти материалы похожи на краски, однако вместо пигментов они содержат высокодисперсные частицы твердых смазочных веществ, которые равномерно распределены в смеси связующих компонентов и растворителей.
Основу покрытий могут составлять дисульфид молибдена, графит, политетрафторэтилен (ПТФЭ) и прочие твердые смазки. В качестве связующих применяются акриловые, фенольные, полиамид-имидные, эпоксидные смолы, титанат, полиуретан и некоторые другие специальные компоненты.
Антифрикционные твердосмазочные покрытия, а также специальные растворители и очистители для предварительной подготовки поверхностей разрабатывает российская компания «Моденжи».
Материалы MODENGY применяются в средне- и тяжелонагруженных узлах трения скольжения (направляющих, зубчатых передачах, подшипниках и т.д.), на деталях двигателей внутреннего сгорания (юбках поршней, вкладышах валов, дроссельной заслонке), в резьбовом крепеже, трубопроводной арматуре, пластиковых и металлических элементах автомобилей (замках, петлях, пружинах, скобах, механизмах регулировки и т.д.), а также в других парах трения металл-металл, металл-резина, полимер-полимер, металл-полимер.
Покрытия MODENGY наносятся однократно на весь срок службы деталей. С их помощью создаются узлы трения, не требующие дальнейшего обслуживания и применения традиционных смазочных материалов.
Антифрикционные покрытия MODENGY отличаются:
- Высокой несущей способностью
- Работоспособностью в запыленной среде
- Низким коэффициентом трения
- Широким диапазоном рабочих температур
- Высокой износостойкостью
- Противозадирными и антикоррозионными свойствами
- Стойкостью к воздействию кислот, щелочей, растворителей и других химикатов
- Работоспособность в условиях радиации и вакуума
Покрытия ложатся тонким слоем, поэтому практически не меняют исходные размеры деталей, зато обеспечивают им необходимый комплекс триботехнических и защитных свойств.
Применение материалов MODENGY позволяет эффективно управлять трением, повышать ресурс и энергоэффективность оборудования.
Оксидные защитные пленки
Оксидирование – это окислительно-восстановительная реакция металлов, которая возникает благодаря их взаимодействию с кислородом, электролитом или специальными кислотно-щелочными составами. В результате этого процесса на металлических поверхностях образуется защитная пленка, которая увеличивает их твердость, снижает риск образования задиров, улучшает приработку деталей и повышает срок их службы.
Оксидирование используется для получения защитных и декоративных покрытий, а также для формирования диэлектрических слоев. Различают химические, анодные (электрохимические), термические, плазменные и лазерные методы этой обработки.
Резиновые защитные покрытия
Гуммирование, или создание защитных покрытий из резины или эбонита, помогает защитить трубопроводы, химические аппараты, резервуары для перевозки и хранения химических веществ от воздействия агрессивных сред.
Защитное покрытие может быть сформировано из мягкой или твердой резины. Консистенция контролируется добавками серы: мягкая содержит от 2 до 4 % этого вещества, твердая – от 30 до 50 %.
Покрытие наносится на предварительно очищенные и обезжиренные поверхности. Скопившийся после обработки воздух выдавливается валиком. В качестве заключительного этапа гуммирования проводится вулканизация изделий.
Резиновые покрытия являются хорошими диэлектриками, обладают стойкостью ко многим кислотам и щелочам (но не к сильным окислителям). Из существенных недостатков резиновых покрытий можно выделить их старение со временем.
Смазки и пасты
При длительном хранении и перевозке металлоизделий в качестве защитных покрытий могут использоваться специальные смазки и пасты – они препятствуют попаданию на поверхности влаги, пыли и различных газообразных веществ, наносятся кистью или методом распыления.
Консервационные материалы изготавливаются на основе минеральных масел (вазелинового, машинного) и воскообразных веществ (воска, парафина, мыла). Очень популярны смазки, в состав которых входит 5 % парафина и 95 % петролатума (смеси парафинов, масел и минеральных восков – церезинов).
Главный недостаток паст и смазок, применяющихся в качестве защитных покрытий, состоит в том, что целостность образовавшейся пленки легко нарушить. Именно поэтому лучшей альтернативой пластичных составов являются антифрикционные твердосмазочные покрытия.
Для поддержания здоровья важно не только питаться полезной пищей и обеспечивать организму посильные физические нагрузки. Посуда, в которой продукты проходят кулинарную обработку, может «насытить» еду опасными химическими соединениями. Важно соблюдать правила эксплуатации кухонной утвари в зависимости от того, из каких материалов она изготовлена.
Антипригарное покрытие представляет собой вещество, называемое политетрафторэтиленом (более простое и привычное название материала – тефлон).
Технология, изначально используемая для военных разработок, со временем получила распространение и в быту. Так, сковорода с данным покрытием имеет гладкую поверхность, требует добавления меньшего количества масла при жарке, не склонна к коррозии, ее легко чистить.
В целом, такая посуда безопасна, пока дело не касается нагревания ее до очень высоких температур. Когда антипригарное покрытие перегревается, молекулы тефлона начинают выделять перфтороктановую кислоту, по сути, являющуюся канцерогеном.
Вещество принадлежит к семейству перфторированных соединений. Оно содержится не только в покрытии посуды с антипригарным эффектом, но и стенках духовки, микроволновой печи, пакетов, в которые обычно упаковывают фастфуд, есть эта кислота в шампуне и даже в составе тканей для пошива одежды.
Из всех этих источников элемент поступает в организм, провоцируя развитие опухолей, ожирение, проблемы со щитовидной железой, работой печени, почек, вызывая бесплодие. Период полураспада перфтороктановой кислоты в организме человека составляет около четырех лет.
Меры безопасности при эксплуатации антипригарной посуды
1) Никогда не нагревайте пустую кастрюлю или сковороду.
Когда посуда пуста, разогрев до высоких температур происходит очень быстро, что приводит к высвобождению опасной для здоровья перфтороктановой кислоты.
2) Следите за температурой.
Критическим показателем является температура нагревания посуды до 250С. Кажется, что это очень высокий показатель, но на деле достигается это значение очень быстро.
Готовьте пищу при низкой и средней интенсивности нагрева. Даже при невысоких температурах покрытие позволит получить желаемую корочку, поэтому нет смысла разогревать емкость сильнее.
При использовании электрических плит выбирайте те, варочная панель которых разогревается медленно, дольше поддерживает стабильную температуру.
3) Пользуйтесь вытяжкой.
Это уменьшит вероятность поглощения вредных для здоровья паров, выделяющихся при нагревании посуды.
Включайте вытяжку, даже если приготовление пищи производится на малом или среднем огне.
4) Выбирайте более тяжелые кастрюли и сковородки.
Такая посуда разогревается медленнее (а значит, синтеза опасных для здоровья веществ не происходит). При этом она лучше сохраняет тепло и позволяет готовить блюда даже при небольшой температуре.
5) Не используйте для чистки посуды абразивы.
Они царапают антипригарное покрытие, вследствие чего в организм попадают частички химических веществ, которые, естественно, не могут им усвоиться и превращаются в токсичные отходы. Поэтому от посуды, покрытие которой уже повреждено, необходимо избавиться.
6) Меняйте любимые сковородки каждые два года.
Данная мера может показаться расточительством, но она не лишняя – даже при бережном обращении спустя два года покрытие становится небезопасным.
Выходом может быть чередование кастрюль и сковородок вместо использования одной и той же утвари ежедневно.
Альтернативой популярному тефлону является использование давно знакомой посуды из чугуна. Она обладает рядом свойств, что делает ее незаменимой для применения всеми, кто придерживается здорового питания.
Преимущества посуды из чугуна
1. В ней нет опасных сложных веществ.
Даже при высоких температурах с поверхности такой посуды не выделяются вредные для здоровья вещества.
Чугун чрезвычайно прочен, он также отлично держит тепло и выдерживает более высокие температуры.
2. Обладает антипригарными свойствами.
При использовании чугунной посуды достаточно небольшого количества масла. Главное — хорошо разогреть посуду и масло, прежде чем добавлять продукты.
Масло при этом проходит процесс полимеризации, связываясь с поверхностью металла и наделяя посуду из чугуна антипригарными качествами.
3. Использование посуды из чугуна увеличивает поступление в организм железа.
Приготовление пищи в такой посуде, особенно, если это блюда, содержащие кислоту (к примеру, томатный соус), способствует насыщению продукта железом, которое перекочевывает в организм. Данное свойство стоит учесть тем, у кого рацион и так насыщен железом (например, велико потребление красного мяса и темной зелени). В таком случае чугунной посуде лучше предпочесть керамическую или из нержавеющей стали. Кроме того, дети до трех лет очень чувствительны к токсичности железа, его переизбыток может вызвать рвоту и диарею.
Антипригарная посуда хороша для приготовления «быстрых» блюд: яичницы, омлета, оладий, разогрева пищи. Когда же требуется многочасовая кулинарная обработка, особенно, при высоких температурах, стоит выбрать старый добрый чугун – пища в такой посуде приобретет отличный вкус и не представляет опасности для организма.
Покрытия наносят на изделия из различных материалов для защиты от коррозии, придания изделиям декоративного вида, создания специальных поверхностных свойств (электропроводимости, теплопроводности, электроизоляционных магнитных и немагнитных свойств, светоотражающей или светопоглощающей способности, износостойкости и др.).
Покрытия могут быть металлическими и неметаллическими неорганическими (оксидные, фосфатные, фторидные и др.), пластмассовыми, резиновыми, лакокрасочными.
При выборе покрытой необходимо учитывать их назначение, условия эксплуатации, материал детали, свойства и характеристику покрытий, способ нанесения покрытий, допустимость и недопустимость контактов сопрягаемых материалов.
Условия эксплуатации металлических и неметаллических органических покрытий делят на группы: легкие Л; средние С; жесткие Ж; очень жесткие ОЖ. Характеристики условий эксплуатации приведены в ГОСТ 306-85. Эти покрытия классифицируют по способу получения, материалу, физико-механическим и декоративным свойствам (табл. 56-5.59).
Защитные свойства покрытий зависят от возможности взаимодействия материалов покрытая и детали. Основные свойства металлических и неметаллических неорганических покрытий и их назначение приведены в табл. 59-5.61, технология нанесения покрытий и методы контроля качества — в ГОСТ 16976-71.
Таблица 56. Обозначение способов нанесения покрытий
Способ получения покрытия | Обозначение | Способ получения покрытия | Обозначение |
Катодное восстановление | — | Металлизационный | Мет |
Химический | Хим | Конденсационный | Кон |
Анодное окисление | АН | Контактный | Кт |
Горячий | Гор | Вжигание | Вж |
Диффузионный | Катодное распыление |
Таблица 57. Обозначение металлических покрытий
Материал покрытия | Обозначение * | Материал покрытия | Обозначение * |
Железо | Ж | Серебро | Ср |
Золото | Зл | Серебро — сурьма | Ср-Су |
Золото — серебро | Зл-Ср | Серебро палладий | Ср-Пд |
Золото — сурьма | Зл-Су | Хром | X |
Индий | Ин | Цинк | Ц |
Кадмий | Кд | Платина | Пл |
Кобальт | Ко | Палладий | Пд |
Медь | М | Родий | Рд |
Медь — олово | м-о | Рутений | Ру |
Медь — олово — цинк * | м-о-ц | Свинец | с |
Медь — цинк | м-ц | Титан | Ти |
Никель | н | Никель вольфрам | Н-В |
Никель — кобальт — фосфор | Н-Ко-Ф | Цинк — никель | Ц-Н |
Олово | о | Оксиды | Оке |
Олово -висмут | О-Ви | Фосфаты | Фос |
Олово — кобальт | О-Ко | Алюминий | А |
Олово — свинец | о-с | Золото — платина | Зл-Пл |
Олово — цинк | о-ц | Алюминий — цинк | А-Ц |
Олово — никель | о-н | Рений | Ре |
* В обозначение покрытий, состоящих из сплава, включают максимальное процентное содержание первого или первого и второго компонентов сплава (в случае трехкомпонентного сплава). Например, медно-оловянно-свинцовое покрытие с массовой долей меди 70-78 % ; олова 10-18 % и свинца 4-20 % обозначают М — О — С (78; 18). |
Таблица 58. Обозначение признаков, характеризующих физико-механические свойства покрытий
Признак покрытия | Обозначение |
Твердое | ТВ |
Электропроводное | э |
Электроизоляционное | эиз |
Таблица 59. Обозначение видов дополнительной обработки покрытий
Вид дополнительной обработки покрытия | Обозначение | Вид дополнительной обработки покрытия | Обозначение |
Фосфатирование | фос | Г идрофобизирование | гфз |
Хроматирование | хр | Пропитка маслом | прм |
Оксидирование | окc | Наполнение в воде | НВ |
Оплавление | опл | Нанесение лакокрасочного покрытия | лкп |
Пропитка | прп |
Таблица 60 Свойства и назначение металлических покрытий
Покрытие | Способ получения | Свойства покрытий | Назначение |
Цинковое | Диф, Мет, Гор, катодное восстановление | 45-50 НВ; интервал рабочих температур -70÷250 °C; обладают хорошим сцеплением с деталью; хорошо работают на изгиб; низкая износостойкость | Защита от коррозии стали, чугуна, меди и ее сплавов |
Кадмиевое | Катодное восстановление | 12—40 НВ; интервал рабочих температур ±60° С; обладают высокой пластичностью, хорошо паяются, выдерживают изгиб, развальцовку, вытяжку, хорошо притираются, устойчивы в морской среде, щелочных растворах, неустойчивы в среде сернистых газов, масел, бензина | Защита от коррозии, в том числе в морских условиях; для обеспечения притирочных свойств деталям при сборке |
Никелевое | Хим, катодное восстановление | 150-600 НВ; легко полируются; коррозионно- стойкие при температурах до±650° С | Защита от коррозии пружин, корпусов и других деталей; декоративная отделка; придание поверхностной твердости, получение светоотражающей или светопоглощающей (черный никель) поверхности. Придание магнитных свойств (Н-Ко) |
Хромовое | Диф, катодное восстановление | 750-110 НВ; химически стойкие, за исключением среды соляной кислоты, галогеноводородных соединений, устойчивы в условиях тропического климата | Защита от коррозии, декоративная отделка, увеличение твердости деталей, работающих на трение; получение светопо- глощающей (черной) или светоотражающей поверхности. Обеспечение способности к пайке, электропроводимости, экранирование от магнитного потока |
Медное | Хим, Мет, Вж, катодное восстановление | 60-150 НВ; электрическое сопротивление при 18°С равно 1,682·10-6 Ом-см; обладают высокой прочностью сцепления, эластичностью, выдерживают глубокую вытяжку, развальцовку, хорошо паяются, полируются, быстро окисляются | |
Оловянное и его сплавами | Хим, Гор, Мет, катодное восстановление | 15-20 НВ; эластичны; устойчивы к сероводороду, органическим кислотам, воздействию тропического климата; выдерживают изгибы, вытяжку, развальцовку | Защита при азотировании, гуммировании, защита от коррозии, обеспечение способности к пайке (О-Вп); декор, отделка (О-Н) |
Серебряное и его сплавами | Хим, Вж, катодное восстановление | 50-150 НВ; электрическое сопротивление при 18°С равно 1,5·10-6 Ом-см; отражательная способность свежего покрытия 90-95%; хорошо паяются; износостойкость пониженная; у сплавов Ср-Су твердость до 22 НВ; тускнеют и темнеют в атмосфере серы, хлора, аммиака | Улучшение электропроводимости, износостойкости (Ср-Су, Ср-П); обеспечение отражательной способности |
Золотом и его сплавами | Хим, катодное восстановление | 40-100 НВ; электрическое сопротивление при 18°С равно 2,213·10-6 Ом-см; обладают высокой теплопроводностью, хорошо обеспечивают сварку. Сплавы Зл-Ср, Зл-Н, Зл-К износостойки и обладают твердостью НВ до 200 | Снижение переходного сопротивления контактов; повышение их износостойкости |
Палладиевое | То же | 200-350 НВ; электрическое сопротивление при 18 °C равно 10,8·10-6 Ом-см; в контакте с пластмассами на покрытии образуются темные пленки, увеличивающие переходное сопротивление | Обеспечение электропроводимости, снижение износостойкости контактов |
Родиевое | » | 400-800 НВ; отражательная способность 73- 75%; покрытия стойки к кислотам, щелочам | Повышение электропроводимости, износостойкости, отражательной способности |
Таблица 61. Свойства и назначение неорганических неметаллических покрытий
Покрытие | Материал деталей | Свойства | Назначение |
Оксидное | Сталь, медь и ее сплавы, магниевые сплавы | Защитные свойства невысокие, повышаются при обработке покрытий маслами, лаками, гидрофобизирующими жидкостями | Межоперационное хранение; декоративная отделка и защита от коррозии (медь, магний и их сплавы) |
Окисно-фторидное; окисно- фосфатное | Алюминий и его сплавы | Обладают эластичностью, хорошей адгезией с металлом; окисно-фосфатное покрытие неэлектропроводно, является хорошим грунтом под окраску | Декоративная отделка и защита от коррозии |
Хроматно- фторидное | То же | Обладают токопроводящими свойствами, стабильностью переходного сопротивления, являются хорошим грунтом под окраску, механически непрочны | Обеспечение стабильного переходного сопротивления |
Фосфатное | Стали | Обладают высоким электрическим сопротивлением, термостойкостью до ±300 °C, не подвергаются пайке и сварке; защитные способности появляются после дополнительной обработки маслами, лаками | Защита от коррозии, создание непроводящего поверхностного слоя |
Пассивное | Стали, медь и ее сплавы | Для повышения коррозионной стойкости применяют дополнительную пропитку маслами, лаками | Защита от коррозии |
Окисное анодизационное | Алюминий и его сплавы; медь и ее сплавы, магниевые сплавы, титан и его сплавы | Твердость покрытия на алюминии и его сплавах 28 44 НВ, электроизоляционные покрытия имеют пробивное напряжение до 600 В; электрическая прочность возрастает при пропитке покрытия лаками; эмалевые пленки на алюминии и окисные на титане обладают износостойкими свойствами. | Защита от коррозии, придание электроизоляционных свойств; получение светопоглощающей поверхности (медь), защита от задиров при трении (титан), грунты под окраску |
Таблица 62 Пластмассовые и резиновые покрытия
Материал | Толщина покрытия, мм | Грунт под покрытие | Температура нагрева °C, в зависимости от метода нанесения покрытия | δ, % | Рабочая температура, °C | Покрытие стойкое в среде | Поверхности детали | |||||||||
Н | П | СВ | к | щ | о | б | с | в | н | д | т | |||||
Полиэтилен ВД | 0.1-1 | 240 | 200 | -50÷100 | + | + | — | + | + | + | + | + | ||||
Полиэтилен НД | 0.1-1 | — | 280 | 220 | 200 | -50÷100 | + | + | — | + | + | + | + | + | ||
Полиизобутилен ПГС | 0,5-2 | Клей 88-Н | 20 | 200 | -40÷80 | + | + | — | — | + | + | |||||
Полипропилен | 0.1-1 | — | 250 | 200 | -40÷150 | + | + | — | + | + | + | + | + | + | ||
Винипласт | 0,3-1 | хгс | 170 | 15 | -30÷70 | + | + | + | + | + | + | — | — | |||
Поливинилхлоридная паста | 0.1-1 | — | 160 | 100 | -30÷70 | + | + | + | + | + | + | + | + | + | ||
Фторопласт-4Д, 4ДП | 0,05 | 370 | 75 | -200÷250 | + | + | + | + | + | + | + | — | + | |||
Фторопласт-3, ЗМ | 0,15 | 330 | 75 | -100÷120 | + | + | + | + | + | + | + | — | + | |||
Масса на основе поливинилбутираля ПНФ-12, ТПФ-37 | 0.1-1 | — | 320 | — | 240 | 50 | -40÷120 | + | + | — | + | — | — | + | + | + |
Капрон полиамид П-68 полиамид П-АК-7 | 0,1-1 | — | 260- 300 | — | 220 | 30 | -40÷120 | — | + | — | + | + | + | + | + | + |
Эпоксидная смола с стекловолокном | 0,5-2 | — | 20 | — | — | 10 | -40÷100 | + | + | — | + | + | + | + | — | — |
Сырая резина на каучуках | ||||||||||||||||
СКВ, СКС | 0,5-2 | Клей лейконат | — | — | 150 | 200 | -40÷90 | + | + | — | — | + | + | + | — | + |
СКН-40 | 0.5-2 | То же | 150 | 200 | -40÷90 | + | + | + | + | + | + | + | — | + | ||
Жидкий найрит | 0.5-2 | — | 20 | — | — | 200 | -40÷90 | + | + | + | + | + | + | + | — | — |
Условные обозначения:
|
Лакокрасочные материалы — многокомпонентные составы, способные при нанесении тонким слоем на поверхность изделий высыхать с образованием тонкой пленки, удерживаемой силами адгезии. Применяют для получения защитных, декоративных и электроизоляционных покрытий на различных изделиях (табл. 64).
Обозначения лакокрасочных материалов в зависимости от наименования смол, эфиров, целлюлозы и масел, входящих в состав пленкообразующих веществ, приведены в табл. 65, а классификация покрытий по внешнему виду в табл. 66.
По составу и назначению лакокрасочные материалы подразделяют на лаки, грунтовки, шпатлевки, краски, в том числе эмали (табл. 65).
Таблица 63
Группа | Обозначение | Группа | Обозначение |
Атмосферостойкие | 1 | Маслобензостойкие | 6 |
Ограниченно атмосферостойкие (под навесом и внутри помещений) | 2 | Химически стойкие | 7 |
Термостойкие | 8 | ||
Водостойкие | 4 | Электроизоляционные | 9 |
Специальные | 5 | Консервационные | 3 |
Таблица 64 Классификация лакокрасочных материалов по составу пленкообратователя (ГОСТ 9825—73)
Наименование | Обозначение | Наименование* | Обозначение |
Канифольные | КФ | Меламинные | МЛ |
Битумные | БТ | Мочевинные | МЧ |
Глифталевые | ГФ | Фенолалкидные | ФА |
Фенольные | ФЛ | Эпоксидные | ЭП |
Полиэфирные ненасыщенные | ПЭ | Эпоксиэфирные | ЭФ |
Алкидно- и масляностирольные | МС | Дивинилацетиленовые | ВН |
Полиуретановые | УР | Поливинилацетиленовые | ВЛ |
Полиакриловые | АК | Масляные | МА |
Сополимерно-акриловые | АС | Кремнийорганические | КО |
Нитроцеллюлозные | НЦ | Полиамидные | АД |
Эгилцеллюлозные | ЭЦ | Пентафталевые | ПФ |
Перхлорвиниловые | МВ | Фторопластовые | ФП |
Сополимерно-винилхлоридные | ХС | ||
Примечание. *Приведены наименования смол, эфиров, целлюлозы, масел. |
В обозначение марки лакокрасочного материала входят буквенное обозначение группы (табл. 65) и несколько цифр, первая из которых указывает назначение материала, а остальные составляют порядковый номер регистрации материала. Например: Эмаль ХВ-16 — перхлорвиниловая эмаль (ХВ), атмосферостойкая 1, регистрационный номер 6; грунтовка ГФ- 020 — глифталевая ГФ грунтовка 0, регистрационный номер 20.
В обозначении покрытий на изделии указывают дополнительно условия эксплуатации (ГОСТ 104-79) и требования к внешнему виду покрытия (табл. 66).
Таблица 65. Свойства и назначение грунтовок и шпатлевок
Наименование, марка (ГОСТ, ТУ) | Цвет* | Режим сушки | Свойства и назначение | |
°C | длительность | |||
Грунтовки | ||||
Сополимеры винилхлорида: ХС-010 (ГОСТ 9355-81) | К-К | 18-23 60 | 1ч 0,5 ч | Наносят на черные металлы, медь и ее сплавы, под перхлорвиниловые и сополимерные эмали в комплексе химически стойких, атмосферостойких, масло- и бензостойких покрытий. Фосфатирование |
ХС-059 (ГОСТ 23494-79) | К-К | 18-23 | 24 ч | Наносят на черные металлы, алюминий и его сплавы под сополимерные и перхлорвиниловые эмали в комплексе химически стойких и атмосферостойких покрытий |
Глифталевая ГФ-0119 (ГОСТ 23343-78) | К-К | 18-23 | 12 ч | Наносят на черные металлы, медь и ее сплавы под различные эмали; обладают удовлетворительной противокоррозионной стойкостью, маслостойкостью |
100- 110 | 35 мин | |||
Фенолно-формальдегидные ФЛ- ОЗК. ФЛ-ОЗЖ (ГОСТ 9109-81) | К-К | 10-23 | 12 ч | Наносят под различные эмали; обладают пов? |